
Joseph and the Amazing Technicolor Dreamcoat
Utah Shakespeare Festival 2019
Director: Brad Carroll
Scene Design: Jason Lajka
Lighting Design: William C. Kirkham
Costume Design: K.L. Alberts
Technical Director: Thomas K Fagerholm
Assistant Technical Director: Daniel Bennett

Model: Jason Lajka
Realizing the Designer's Intent
Set Design by Jason Lajka, known for his film work as Art Director for Wendell & Wilde, Set Designer for Coraline, and concept model work on ParaNorman.

Photo: Karl Hugh

Rendering by Jason Lajka
For the 2019 Utah Shakespeare Festival summer season, two shows played in repertory on the Randall Theater stage: Joseph and the Amazing Technicolor Dreamcoat and Hamlet. The sets changed over in about one hour with just 6 crew members. To meet this challenge, I assigned two of my Assistant Technical Directors to one production each and my third ATD to serve as the shop supervisor and load-in . This way there would be a lead on each show, and I could serve as the bridge between the two.
The primary feature of this set was the stained-glass cyclorama and translucent light box set pieces. Each of the light box walls were 20 feet tall and covered in a synthetic cyclorama fabric.
A video clip of this production can be found HERE.
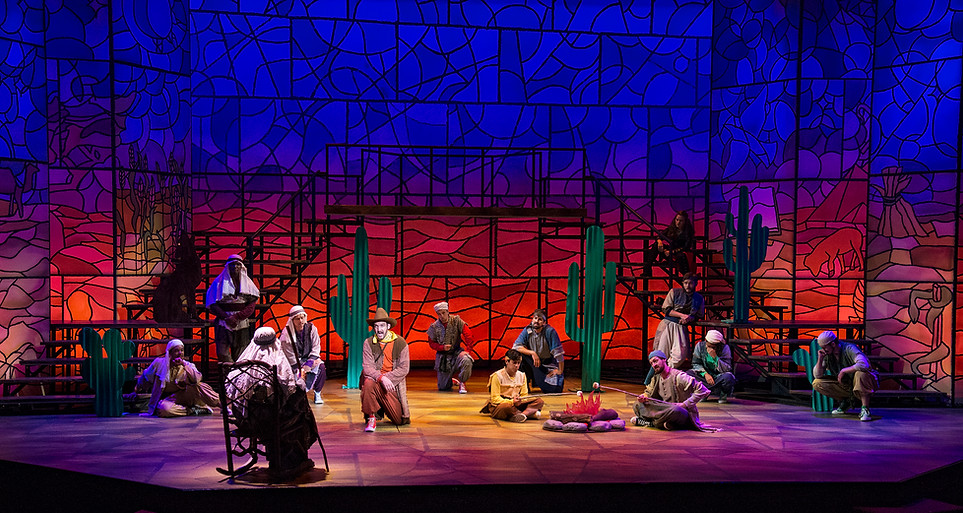
Photo: Karl Hugh
PRODUCTION BID: LABOR & MATERIALS
Bidding labor and materials in the pre-season in a major responsibility for the technical director at USF.
The main page at left gives a summary breakdown of the budget and labor expenses overall and for each unit.
Click on the BID image for a full PDF version.
At the end of the season, we reconcile all materials and expenditures to check how close our estimates were. On Joseph, we ended the season under budget for both materials and labor. This was a marked increase from the previous year, and much could be owed to the number of returning management and carpentry staff. This led to efficiencies in sourcing materials, reusing stock items, and labor efficiencies.

TRACKING PROGRESS & PRIORITIES
Excel Document used to track priority and progress for each scenic unit.

The Primary List Excel document also tracked daily carpenter assignments. This was something new to USF that I brought from my experience at Glimmerglass Festival. This second year at USF, we utilized Google Documents for the daily lists to better facilitate shared editing. This helped expedite updates to the list amongst the TDs and ATDs.
PRODUCTION PROCESS

These images show the stretching of the synthetic cyclorama material over the steel frame. The fabric was wrapped around the edges of the frame and stapled to plywood tack strips on the back of the steel frame. This allowed for the fabric treatment to fully cover all the visible sides of the units.
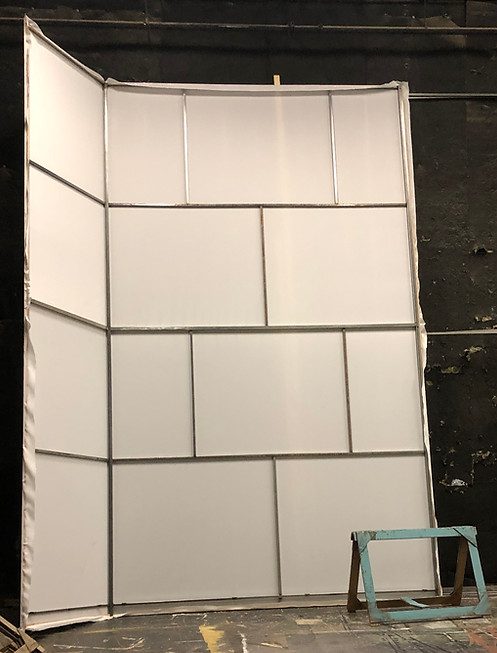

A Fun challenge to this production was the parallelogram nature of the mirrored set pieces. To the left is a picture of my ATD Daniel Bennett and our lead carpenter & welder Doug.
​
When Daniel started that summer, his experience with AutoCAD was primarily from class projects in graduate school at SIU. As the primary draftsperson for Joseph, Daniel quickly developed 3d drafting skills with my guidance. Below is the overview drafting plate he created for the lower stair units.
CLICK TO SEE MORE

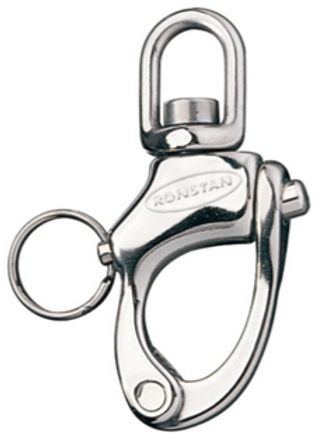
S-Bail Snap Shackle
Westmarine.com
One of the great joys of working as a technical director on productions is solving unique technical challenges. I particularly enjoy the research and development phase as I often learn new techniques and tools from other trades and industries.
​
During the reveal of the technicolor dreamcoat, the design team envisioned the coat flying in from above the stage and the actor quickly stepping into the coat. In order to achieve this effect, we needed a way to safely rig the coat to cables on a batten above the stage and yet be able to be quickly released right in full view of the audience. This required traditional research and collaboration with the costume shop to find construction techniques and hardware that would not be cumbersome and would be reliable.
​
First, I searched the scene shop and properties shop inventories for hardware that might work. I talked with the director of props, the faculty Technical Director at Southern Utah University (where USF is situated), to gather as much information as I could. In the top left corner, you can see a sketch and hardware I presented to the costume designer and costume shop manager both. The clip on the right, a swivel trigger snap, was the preferred of the two I chose to show but still a bit cumbersome to operate.
​
I continued my research which eventually led me to two possibilities, quick release dog clips or s-bail snap shackles. I purchased two of each for the effect to test. In testing, we found that the s-bail snap shackles, typically used on sail boats, was the easiest to operate quickly. In the bottom left is an example of the type of shackle we utilized.

Pharaoh's Entrance
Photo: Karl Hugh

Photo: Karl Hugh
Song of the King
The platform Pharaoh is seen standing on was attached to a cable lift center stage. This cable lift was operated via Creative Connors Showstopper 3 and Spike-Mark automation control system. While this lift was installed several seasons earlier, my ATDs and I did multiple upgrades and fixes to the homemade lift. One upgrade for this unit was to add additional counterweight to the lift to maximize its lifting capabilities.

Randall Theater Stage Lift 3d AutoCAD model.
Robert Anderson, my other ATD, and I spent considerable time cleaning up the original drafting and engineering drawings for the Randall Theater cable lift. The above is our final 3d model that includes modifications we made such as reinforced lift towers, counterweight arbors, mule block stiffeners, and pneumatic locks. This file was cleaned up, documented, and saved for future productions and the scenery director of USF.
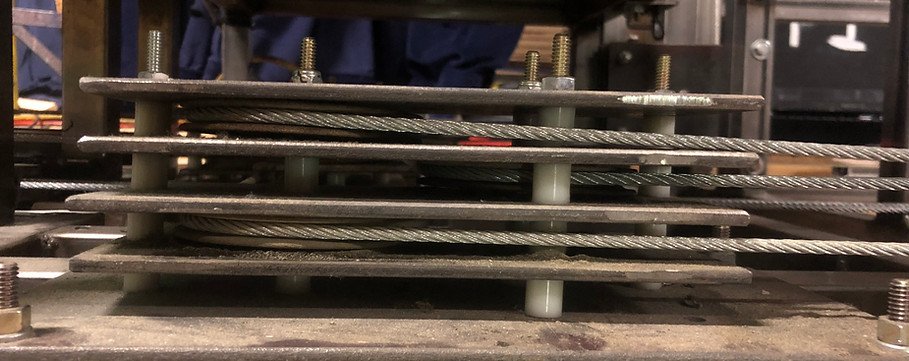

One of the issues we noticed in operation from the previous year, was that the mule blocks that change the direction of the lift and pull-down cables as they go back towards the winch, were not captured at the top and was causing the sheave pack to tilt. This was causing excessive wear on the sheaves and potentially damaging the cables as well. I came up with a remedy that would simply attach to the frame already installed and add support/capture of the top of the sheave stacks. After the adaptation, the fleet angles were corrected, and new sheaves were installed resolving the issue. These images show the issues with the sheaves before the fix.


THE FIX: In these images we see the top plates of the sheave packs captured by the surrounding steel frame. The center pack is captured with a piece of angle iron holding the stack in tension.
-150.jpg)
Sample Drafting
-151.jpg)

Photo: Karl Hugh

Photo: Karl Hugh
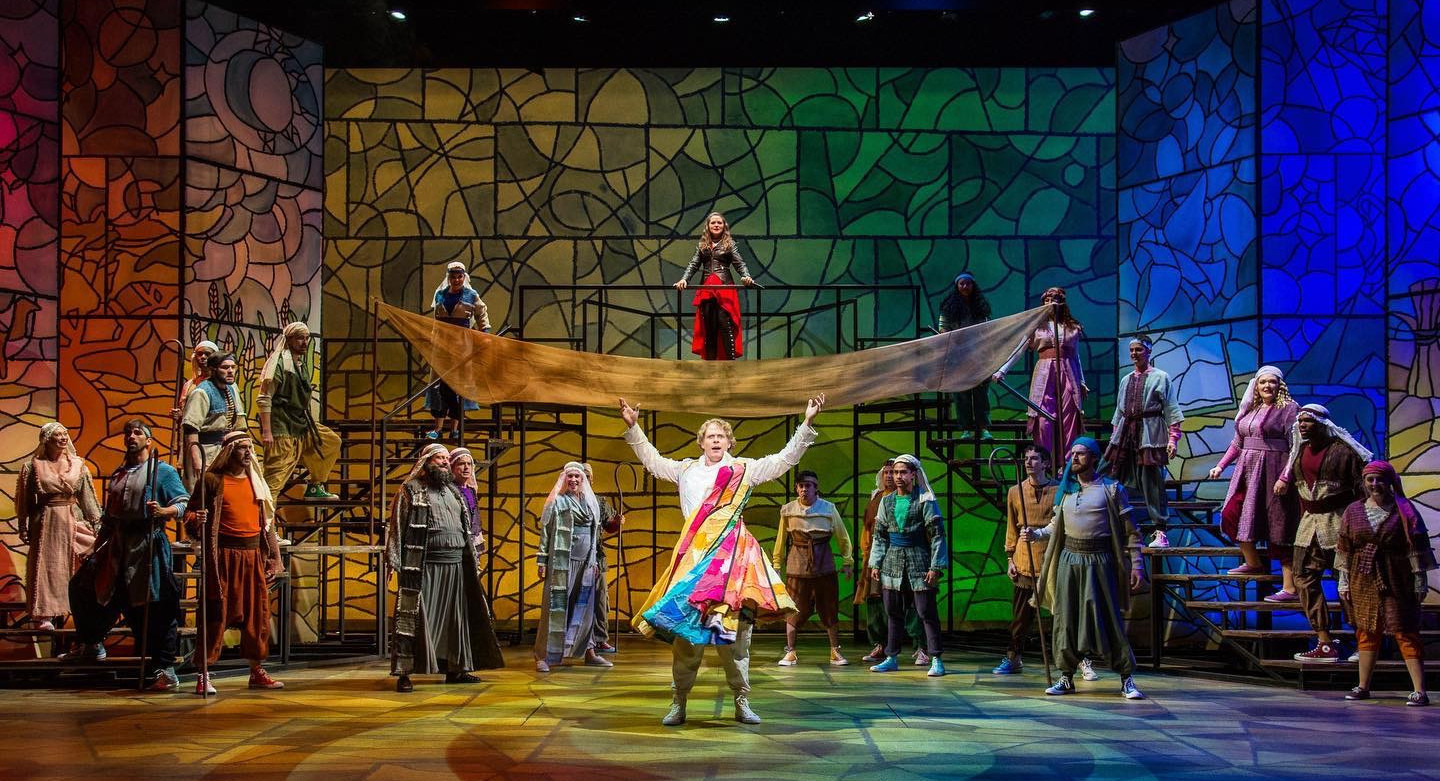